Author: Antoine Le Tullier, Novelis PAE, Voreppe
New generation of “Hands Free” Casting: AUTOPAK® Metal Drive System, Ready for Industry 4.0
The development of hands-free automatic DC casting started at Novelis PAE more than 40 years ago, in the 1970’s. It was mainly driven by safety needs such as keeping the operator away from the pit and protecting him from various risks, in particular from the risk of explosion.
In the 1980’s, major aluminium plants in Europe, such as Aluminium Dunkerque, Alunorf, Constellium Neuf-Brisach, Hydro Neuss and Hydro Hamburg, implemented our AUTOPAK® system, thus enabling safe, hands-free casting.This was the origin of the first automatic, metal level control system for DC casting: Novelis PAE proposes now a further step with AUTOPAK® Metal Drive System. This is a flexible and reliable system based on new, fully digital capacitance sensors and actuators, dedicated to revamping and to new automation projects, paving the way to an Industry 4.0 equipment.
The choice of a reliable CAN Bus solution for a low footprint plug-and-cast solution
A weak point of some existing casting launders is their attached electrical devices. The cables and connectors needed to control these devices are located directly on the launder, in a hot and harsh environment. In some cases, a control cabinet with control modules is located outside the casting pit: this implies connection through sensitive signal cables, which risk damage during the handling of the casting launder. To limit this risk, the control cabinet can be attached directly to the casting launder. However, the cabinet still takes up a lot of space, and this solution is often complicated to implement.
The new metal level control system proposed by Novelis PAE is much more compact: the control modules of the sensors and actuators are directly embedded inside the sensor or the actuator enclosures. Only standard CAN bus and standard power supply cables are used to communicate and control the sensors and actuators from the PLC system.
The choice of this proven and reliable CAN communication network makes the whole system simpler, and it is less sensitive to the environment. It leaves more space on the utility beam above the casting trough, and so more possibilities to implement additional equipment.
Industry 4.0 ready, flexible interface for future evolutions
By using the CAN bus network, sensors and actuators are set up and controlled automatically from the main control interface. This access is also given on line through a Web Server and a dedicated software, called AUTOPAK® Interface, to check and to transmit all data through an internet link.
A specific network hub is available to make the interface between the CAN bus used on the casting launder and the customer’s standard networks communications protocol, such as Ethernet, Profinet or Ethernet I/P, to name but a few (Fig.1).
All the internal parameters can be collected and sent back immediately to the main supervision system. Collecting each parameter together in a large database makes possible a detailed and interactive data analysis. This makes possible predictive maintenance of the components, which can extend the lifetime of the sensors or flow-controller. It creates many possibilities to improve the process by automatically analyzing these data.
New CS-F240 Capacitance Sensor
The principle of the capacitance metal level sensor is based on a double measurement, comparing the capacitance between two electrodes with that between the electrode and the metal surface. Both measurements are permanently compared so as to deduce the metal level. This double measurement makes the system almost insensitive to ambient conditions, and it guarantees a high accuracy of measurement, usually better than 1 mm.
To facilitate use and maintenance, the new CS-F240 Capacitance Sensor (Fig. 2) and the FC-F100 Flow Controller each have their own digital control card built in. Each sensor or actuator also features a quick connector with its own encoding: the system automatically recognizes the strand position. A QR code has been added on the enclosure to facilitate the traceability of the equipment during maintenance procedures.
Since the sensor works close to the liquid metal, an accurate control of temperature is required. A lot of reengineering work has been carried out – and thermal shields added – to improve the thermal protection of the sensor’s sensitive parts. New specially heat resistant connectors have been intensively tested at higher temperature to guarantee their long-term reliability.
The special, heavy-duty electronic components are maintained at a higher and stable temperature, up of 70°C. This solution makes the system and the metal level measure insensitive to ambient temperature variations around the sensor. The temperature increase of the environment does not shorten the lifetime of the sensor control module.
Each sensor is fully calibrated on a factory test bench, and is delivered with its own, specific calibration curve permanently saved in its electronic module. The sensor defines automatically its optimized working position and regulation parameters according to its own calibration curve.
A magnetic linear encoder replaces the sensitive potentiometer for a better stroke measurement accuracy. The previously proven, robust mechanical components have been retained and are common to the sensor and to the flow controller so as to reduce and facilitate maintenance. Since the previous mechanical interface remains the same as in the previous generation, the new CS-F240 is compatible with existing equipment, and easily allows future modernization.
Visual management
A camera system can be added on the pit to help the operator in the cabin to visualize the pit. A simple and robust programmable LED bar graph (Fig. 4) is integrated on each flow controller and sensor. Configured according to the needs of each cast house, it gives the operator an instant view of the sensor status and casting stage. The LED bar graph can also serve as a visual alarm, not only inside the control cabin, but also all around the pit during maintenance works.
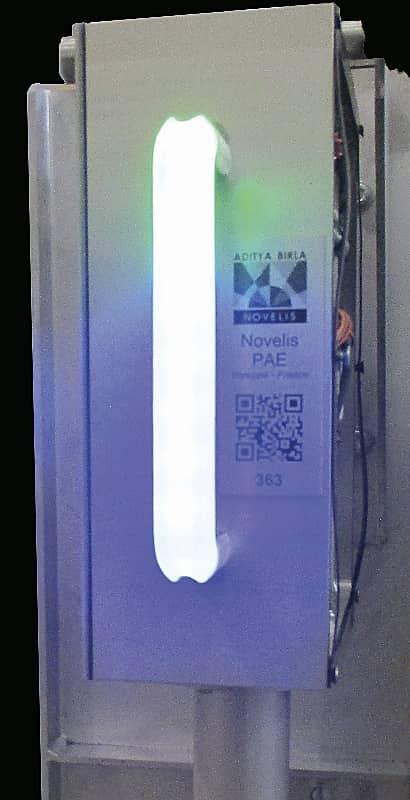
The new AUTOPAK® Metal Drive System was recently implemented at the Alunorf casthouse in Germany. An automatic metal level regulation system was installed on an existing casting pit to modernize it and to replace a manual system. The new generation of sensors and actuators has been successfully tested in real and industrial conditions.
Combining ergonomics, reliability and safety for a better casting process, AUTOPAK® Metal Drive System represents a modern automation solution to revamp cast houses. The new CS-F240 Sensors and FC-F100 Flow Controllers, using the CAN bus field solution proposed by Novelis PAE, give now a large choice of integration and development possibilities, adapted to each cast house project.
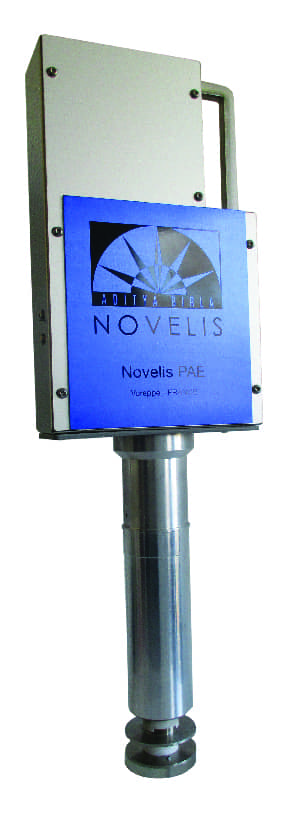
Light and compact FC-F100 Flow Controller
Benefitting from the same mechanical improvements as the sensor, the flow controller’s weight has been drastically decreased to less than 7 kg. Its main dimensions have been halved to facilitate its mechanical integration.
The FC-F100 (Fig. 3) remains intrinsically safe: it integrates a pin self-closing function in case of power shutdown or of emergency stop, thanks to a simple and robust magnetic mechanism. At the beginning of the cast, it automatically detects the so called “closed position” thanks to an automatic self-learning procedure.
The FC-F100 suits an auto predictive PID regulation. It brings a very fast response time and high position accuracy, allowing some short and fast impulsion openings, if this is required by the casting recipes, or by the operator located in the cabin during the cast.
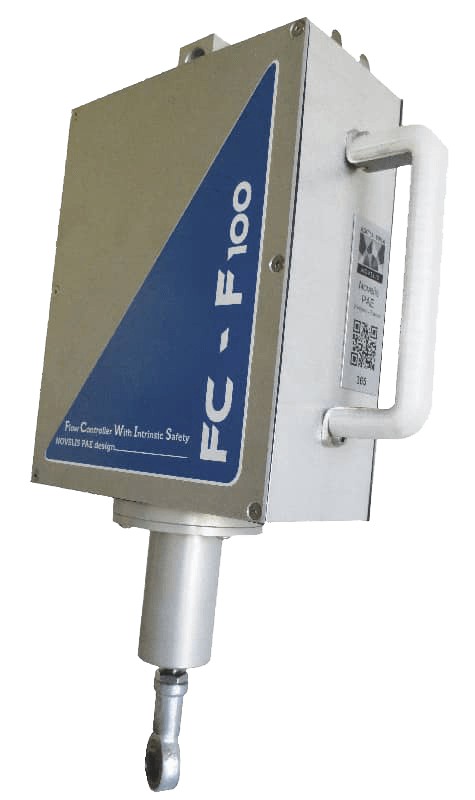