After the successful installation of five continuous casters in 2008, a new contract was signed last year between Assan Aluminyum, a subsidiary of Kibar Group, and Novelis PAE, for the supply of two additional Jumbo 3CM®casters in the Dilovasi plant in Turkey. This investment is part of a major expansion of Assan Aluminyum in the foil and flexible packaging production. The casting lines were installed and commissioned in a very short 3-month period by a joint team of Assan Aluminyum and Novelis PAE.
With these two new lines, Assan Aluminyum is consolidating its leadership in aluminium strip casting with a total of 19 production lines, 12 in the Dilovasi plant and 7 in the Tuzla plant, and strengthening herewith its long term partnership with Novelis PAE as a supplier of casthouse equipment.
The two casters, commissioned in May 2017, have been designed to produce high quality aluminum strip in 1000, 3000, 8000 and 5000 alloys in width up-to 1800mm.
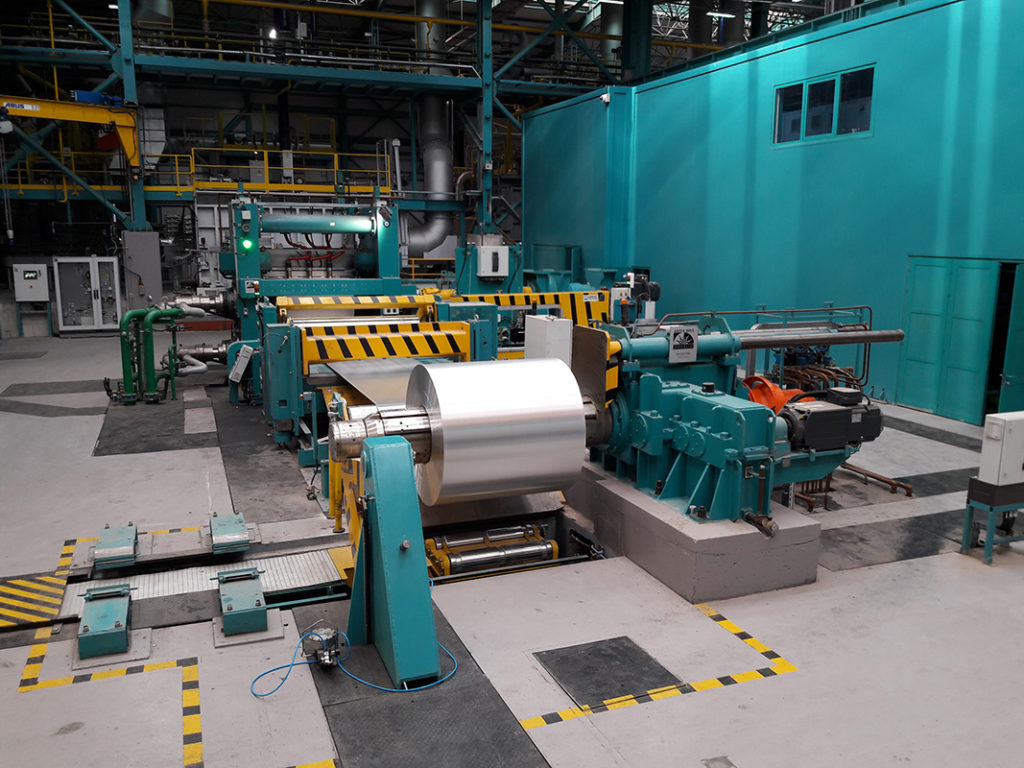
They benefit from several new features in order to:
- improve the quality and consistency of the production,
- make the casting operation and maintenance easier for the staff,
- reduce the downtime
The casters are equipped with Novelis PAE latest technology which includes new AC drives, pressure and roll gap control of the casting rolls, fully motorized tip table, new pinch roll design, automation and process supervision system with new HMI operator interface.
The design and lay-out have been thoroughly reviewed with the customer engineers in order to optimize the operation and facilitate the maintenance of the equipment by detecting easily and early enough a potential defect on the machine.
The quality of the molten metal remains a key point of the final product quality for high end applications. The metal treatment system features the newly developed ALPUR® G3 and a PDBF® 5 deep bed filter. This new generation of ALPUR®integrates many innovations to guarantee a high degassing efficiency but also an easy operation and maintenance of the machine thanks to integrated hatches, sensors, and quick connectors on immersed heater and injectors.
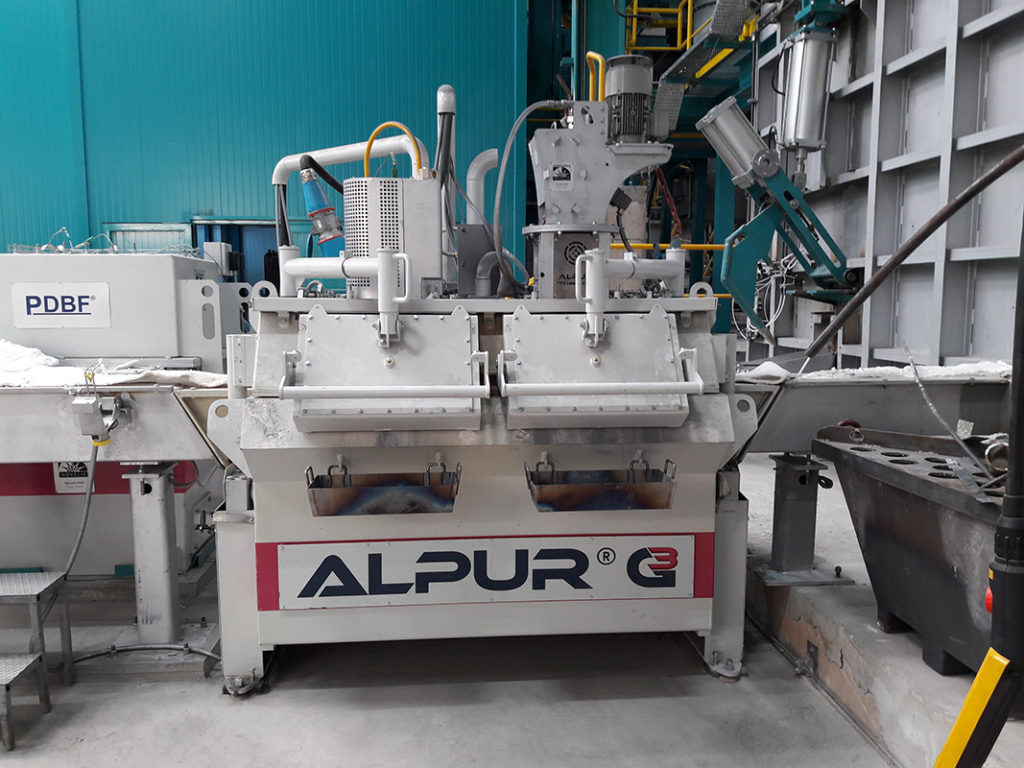
A special attention has been put on the assistance and the training of the operators. Thanks to PAE’s dedicated team of specialists, the installation and commissioning time has been reduced to a minimum ; the two lines started production within 3 months from the delivery on site, insuring a quick and optimized cost-effectiveness to the customer.